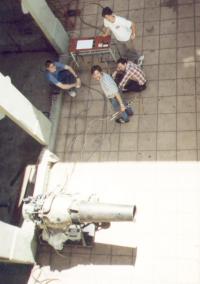
No importa qué tan seria ó ligeramente nos lo propongamos:
parece que estamos condenados a trabajar a rajatabla sin poder cumplir
con los plazos que nos proponemos. Comenzamos a trabajar el 1ro. de Setiembre,
pensando en una rueda de cola nueva, un par de refuerzos
al caballete, un tubo de chorro nuevo, un tanque de combustible nuevo
y un tablero eléctrico que nos permitiera prescindir del arranque con
aire comprimido. Es más, llegaríamos con tiempo suficiente para
intentar una puesta en marcha durante la Semana de la Educación Técnica,
y seguro tendríamos tiempo después de finalizado el período
regular de clases para hacer un medidor de empuje aunque más no fuera
elemental. Aún con el mismo régimen de trabajo del año
anterior, somos el mismo equipo!.
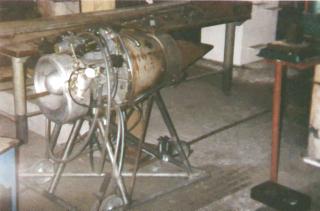
Lo cierto fue que no sólo no pudimos cumplir con la
Semana de la Educación Técnica, tampoco pudimos cumplir con el 10
de Diciembre (Aniversario de la primera puesta en marcha del turborreactor Derwent V), como tampoco el 17 del mismo mes
(Aniversario de la primera puesta en marcha del turborreactor Marboré IIc). Apenas llegamos otra vez al
19 de Diciembre, un par de días antes del fin del Ciclo Lectivo y sin medidor de empuje...
Quizás fuimos un poco (demasiado) optimistas acerca del tiempo que
demandaría cada una de las tareas propuestas, pero los problemas
inesperados que enfrentamos nos costaron días preciosos. Y aunque un
poco tarde, por suerte pudimos concluirlas exitosamente. A continuación las
describimos por casi riguroso "grado de dificultad":
Tubo de chorro
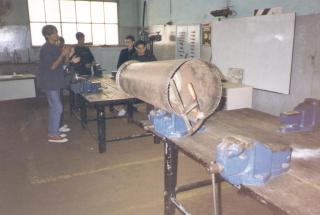
Qué decir de la pieza que cuidadosamente estudiada
en su forma y uniones para ser terminada en tres tardes finalmente nos
demandaría
doce días completos de trabajo?. Aquí
el problema no fue la elección del material (chapa de acero
de 2 mm. de espesor), sino nuestra inexperiencia en el cortado, cilindrado,
plegado y fijado del mismo.
Previamente hicimos un desarollo del tubo
en Autocad, lo único rápido y sin problemas del asunto. El corte
de la chapa debimos hacerlo con discos abrasivos de corte.
Solamente ésta operación nos demandó dos días
completos de trabajo. Cilindramos y plegamos el tubo en el taller de Herrería
y para poder sacar el tubo recién cilindrado de la máquina tuvimos que desarmarla...
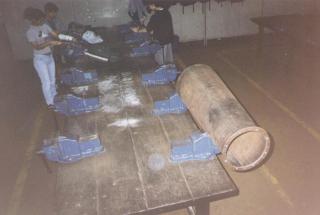
Y la primera impresión del trabajo efectuado era realmente
desesperante: el "tubo" era algo deforme por donde se lo viera y la dureza del material plegado en frío hacía
casi imposible cualquier intento de manipulado ó ajuste. Se nos advirtió muchas veces que
debíamos trabajarlo en caliente, pero la falta de tiempo y equipos nos hizo descartar la idea.
Y terminamos tardando por lo menos el triple de lo necesario en el plegado. Luego tuvimos
que fabricar moldes de madera y acero para llevarlo lentamente a su casi
forma final y terminar de darle la misma durante el montaje sobre
el turborreactor con una herramienta gigante creada para tal fin. Tampoco
fue un problema menor el hacer con un taladro manual los 28 agujeros que sujetan
al tubo sobre el turborreactor. Una cosa es agujerear hojalata y otra
acero de 2 mm. de espesor...
Esperamos no necesitar un tubo de chorro nuevo cada seis meses!
Acelerador
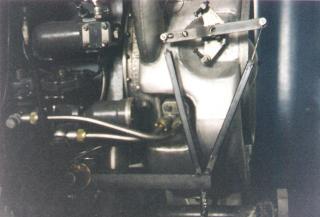
Otra cosa que nos produjo retrasos increíbles fue el poder contar con un sistema de
comando adecuado para regular las RPMs de la máquina. Sabíamos por experiencia del '82
que un comando por cable tipo freno de bicicleta era absolutamente inadecuado (En el Derwent V se habían instalado
motores eléctricos sincrónicos). Y por lo mismo de siempre (falta de tiempo, recursos
y alguien entre nosotros que supiera cómo hacerlo rápido...)
dicha solución se descartó por alguna otra mucho más rápida y económica que demandaría a lo sumo...
diez días más!.
En algún momento se habló de motores paso a paso, y se descartó tan rápido cómo se propuso (mismos motivos de antes).
Nos pusimos a ver las posibilidades de utilizar un sistema de control hidráulico, pero el
costo de adquisición era lisa y llanamente prohibitivo.
Entonces intentamos hacer nuestros propios actuadores. El resultado fue más que interesante si hubiésemos dispuesto de más tiempo
para desarrollarlos. Uno de simple efecto demostró fallar por aplastamiento de las tuberías plásticas que
usábamos, y uno de doble efecto (el más prometedor de los dos) llevado adelante por J. Radesca con cilindros para
aire comprimido fue casi perfecto
de no ser que tenía una carrera de 20 mm. cuando necesitábamos 70 mm. Entre pruebas y por momentos volvíamos al comando de
"tripa" simple y terminamos con algo que sólo un levantador de pesas podía manejar adecuadamente.
Volvimos a comenzar con algo que muchas veces comentamos sin convencimiento y era hacer un sistema
de "tripa" similar al primero, pero
doble (Sistema de tira y afloja). Para el caso demostró ser lo más adecuado, y aún así nos llevó
cuatro días ponerlo a punto.
Cosa a mejorar en el 2001.
Tablero eléctrico
Cuando creímos que después de los problemas de los aceleradores todo estaba encaminado nos volvimos a equivocar.
Teníamos dos problemas básicos con el tablero eléctrico: Encontrar un circuito que supliera de manera efectiva a los elementos
ausentes del original del avión, y todavía peor; encontrar elementos de
costo cero de adquisición que soportaran el amperaje
producido en el arranque. Todo iría montado sobre lo que quedaba de una mesita rota con las patas prolongadas y una superficie
de trabajo de cartón corrugado. No. no estábamos tan pobres. Nos fue ofrecido armar algo mucho mejor por el taller de
Carpintería, pero dado que suponíamos (y ésta vez no nos equivocamos) que haría falta hacer muchas modificaciones sobre
la marcha que finalmente desmerecerían el aspecto final de algo bien hecho; preferimos dejar lo
bien terminado para más adelante.
Tuvimos que cambiar la caja auxiliar de engranajes por el mismo conjunto del
turborreactor para canibalizar, porque comprobamos que el sistema de acople
motor eléctrico auxiliar - compresor no se encontraba en buenas condiciones.
Ésto pasaba inadvertido usando el arranque con aire comprimido.
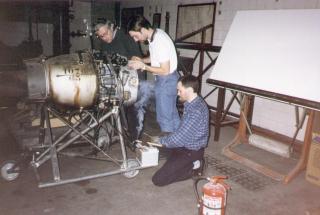
Después necesitaríamos fabricar una resistencia auxiliar para el sistema de arranque que
se usaría solamente durante los primeros 8 segundos del mismo para evitar la rotura de la
caja de engranajes al momento de conectar el motor eléctrico auxiliar.
Decidimos hacerla con alambre nicrom y determinamos el valor necesario experimentalmente.
Puede verse en la foto alguna de las tantas resistencias que no pasaron la prueba.
Pero también resolvimos éste problema.
Después vendría el "circuito" eléctrico definitivo (número III) y dejamos como último trabajo el cableado y conexiones antes de intentar una puesta en marcha.
Recibimos como donación los cables y llaves para el tablero, amperímetro y voltímetro para medidor de RPMs pero perdimos dos días
solamente buscando alguna llave ó mecanismo que pudiera soportar 180 Ampere del arranque sin problemas (y que lógicamente no tuviéramos que pagar...). Como no encontramos, al
final intentamos con llaves de 15 Ampere donadas por el taller de Electricidad. Aguantaron!.
El "Arrancamatic" necesita un replanteo y reconstrucción total para el 2001.
Termocupla y medidor de temperatura de salida de gases
Otra de las cosas con las que aprovechábamos los tiempos muertos cada vez que no teníamos material para continuar con los trabajos era la termocupla.
Todavía no sabemos porqué falló en 1999, pero después de algunas pruebas comenzó a señales de vida nuevamente.
Cambiamos cuatro instrumentos para medir, y como no confiábamos en ninguna de las lecturas que obteníamos
después de otro par de días perdidos terminamos haciendo lo que debimos desde un
principio: llevamos el conjunto termocupla - cable compensado - instrumento de medición
al taller de Cerámica y lo contrastamos contra el indicador de uno de sus hornos.
Tres tomas de datos calentando y enfriando, y el trazado de una "curva de calibración"
(En realidad curva de contraste...) nos dejaron algo más tranquilos acerca del
comportamiento del conjunto.
Otra cosa a mejorar en el 2001.
Tanque de combustible
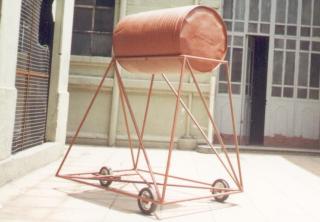
Pocas cosas (ó ninguna) como el tanque de combustible se hicieron tal como se planearon, sin
contratiempos, pudiéndose incluso probar con una maqueta de madera de tamaño real el desempeño del
dispositivo terminado. La idea era hacer algo trasladable a cualquier sitio del Colegio y
que permitiera un cambio rápido del tambor vacío de 200 litros por otro igual pero lleno con
sólo girar hacia atrás 90 grados el reticulado, aflojar un par de bulones, cambiar el tanque,
ajustar de nuevo los bulones y rotar de nuevo el conjunto a su posición normal.
Hay que agregarle un medidor de nivel para el 2001.
Bastidor
Quizás el trabajo más simple de los encarados durante el 2000 fue reforzar el
bastidor existente con miras a poder soportar al máximo posible de RPMs (y por
lo tanto también máximo empuje) del turborreactor , básicamente "rigidizando"
al conjunto con el agragado de "diagonales" sobre las esquinas de la base. Bien sobre mediados
de Diciembre se agregaría el soporte para el (todavía inexistente) medidor de empuje
y la placa de soporte de las baterías.
Mejor terminación y pintura para el 2001...
Rueda de cola del bastidor
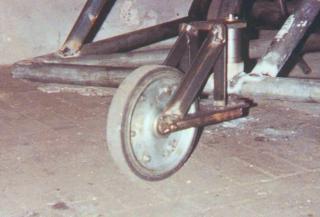
Una vez concluídos los trabajos de refuerzo del bastidor se realizó un soporte nuevo para la rueda
de cola. El utilizado hasta ahora mostraba signos de fatiga en las articulaciones y el
aumento de peso por la inclusión de las baterías en el caballete y los refuerzos sólo iba a empeorar las cosas.
Esperamos que ésta sea la versión definitiva. (Y van tres...)
Con la falta de algunos materiales y/o el efectivo para conseguirlos, el 20 de Noviembre la Asociación Cooperadora del Colegio nos
dona $436 que nos permiten adquirir parte del material que como se verá más adelante demostró ser
fundamental en la puesta en marcha de éste año.
Y después de una semana de decir "mañana lo intentamos" llegamos como fecha y hora
posibles del primer arranque del año al lunes 18 de Diciembre a las 10:00 hs.
Las 10:00 hs. se hicieron las 16:00 hs. y las expectativas creadas (muy a nuestro pesar) no eran pocas. Había
más de 20 personas esperando ver el turborreactor en marcha. No esperábamos
funcionar por más de cuatro minutos porque usábamos el poco
combustible y aceite que habían quedado del año anterior. Con el tablero eléctrico recién terminado y sin probar
no hubo más que intentar la secuencia de encendido.
Primer intento: no hay movimiento alguno del motor de arranque.
Segundo Intento: idénticos resultados.
Motivo: llave general de encendido mal conectada....
Una vez solucionado el inconveniente, el tercero al sexto intento de arranque fueron normales en la primera etapa, pero
siempre nos faltaban las RPMs necesarias en la segunda etapa para poder encender la máquina. Después de varias
revisiones al tablero para encontrar la falla se determinó que otra de las llaves
también estaba mal conectada, pero una vez corregido el problema no había
mejora alguna en el comportamiento del sistema de arranque. Y las cosas ya recordaban bastante a los
primeros intentos de 1982, a pesar que en 1999 la máquina había arrancado al primer intento en condiciones muchísimo
más precarias que las del corriente.
Suficiente por el 18 de Diciembre.
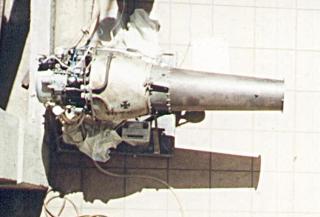
Así que por la mañana del 19 nos dedicamos a seguir más tranquilos el cableado
y efectivamente, "descubrimos" que la misma llave del día anterior seguía mal
conectada. Bromas aparte para con el (i)rresponsable que cometió dos veces el
mismo error, realizamos algunas pruebas sustituyendo al sistema de arranque por una resistencia fija que nos
permitió ahora sí tener la seguridad de que todo estaba en orden y preferimos posponer la puesta
en marcha hasta las 16:00 hs., ya que varios de los integrantes del equipo de trabajo se encontraban ausentes con aviso.
Llegada la hora, bromeamos con el jefe de talleres de Mecánica Ciclo Superior acerca del número de intentos del arranque.
Alguien a quien mejor no identificar dijo: "Arranca de primera...". Y no era que no supiera lo que decía. El jefe, más prudente contestó: "Ojalá...".
Y había casi tanta gente como el día anterior...
Lo cierto es que lanzada la secuencia de arranque la primer etapa del mismo se
supera con holgura, pero al comenzar la segunda etapa el motor de arranque
se para...
Como ya no teníamos más elementos de juicio a nuestra disposición, decidimos dar
por terminadas las pruebas del día (así lo hicimos saber a los presentes) y
volver a revisar por enésima vez el circuito eléctrico y las conexiones del tablero.
Dicha tarea la dejamos a E. Álvarez y J. Di Iorio, ya que no habían estado involucrados de cerca con el tablero y
entonces podría ser más fácil que encontraran algún error que se nos hubiera escapado.
Después de revisar todo por una hora se llega como única posibilidad del problema
a que las baterías empleadas
estuvieran descargadas. Pero si había algo en lo que tuvimos cuidado fue en cargar las baterías en todo momento!.
En fin, a cargarlas otra vez por una hora y probar arrancar utilizando por primera vez el cargador y carro de arranque
comprados con la donación de la Asociación Cooperadora.
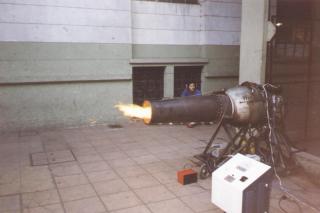
A las 18:50 hs. decidimos medir el estado de carga de las baterías pensando más en el 20 de Diciembre que otra cosa.
Y para efectuar la medición no había otra forma que iniciar la secuencia de arranque
por tres segundos y cortarla.
Como antes de los tres segundos escuchamos cómo el sistema primario de
encendido se había activado, y los resultados de la medición fueron buenos;
decidimos ahí mismo intentarlo otra vez.
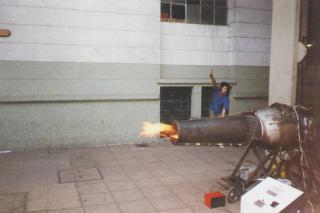
Con cada persona en su sitio, y Jorge Radesca en los comandos; a las 18:52 hs. lanzamos la secuencia de arranque y ésta vez después de 35 segundos el
Marboré estaba funcionando por sus propios medios. Después de obtener el régimen estable de marcha verificamos que
teníamos lectura de presión de aceite en el manómetro (2 kg/cm2), lectura de temperatura indirecta con la termocupla (380 °C)
y número de vueltas indirecta con el generador usado como taquímetro (6 000 RPM).
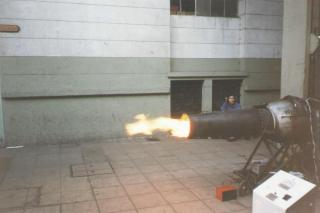
Como contábamos con un nivel mínimo de aceite, y quizás un combustible no tan adecuado cómo se requiere;
decidimos al minuto de marcha apagar el turborreactor, porque además los valores obtenidos en las lecturas
de los instrumentos eran tan bajos comparados con los del manual de mantenimiento que
pensamos que ningún instrumento funcionaba correctamente... (
Nota: sensación que confirmaríamos
un año más tarde! Ver Así nos fue en 2001)
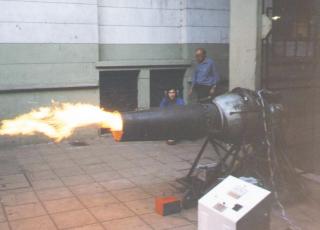
Y al igual que el año anterior, la válvula de cierre de combustible volvió a estar mal colocada y el turborreactor recién
se detuvo cuando agotó el combustible que quedaba en la línea de alimentación.
Puede verse en la secuencia de fotos el arrancador y un cargador adicional contribuyendo al arranque
y cómo a medida que la máquina entra en régimen la llama del tubo de chorro se hace cada vez más
corta hasta desaparecer dentro del tubo de chorro.
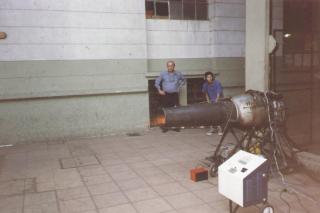
Ésta vez nuestro fotógrafo (Alejandro Flagel, al igual que el año anterior) estuvo realmente inspirado, sacando una secuencia notable
del arranque.
Final por éste año. La alegría de los más jóvenes era indescriptible y ya pensaban en repetir lo hecho el 21 y 22
de Diciembre.
Pero los más ancianos del grupo (entre los que se encuentra el que escribe) resolvimos que era
mejor asegurarse que las lecturas obtenidas en los instrumentos fueran correctas y conseguir JP1 y
aceite para turbinas adecuados para volver a intentarlo en el 2001.
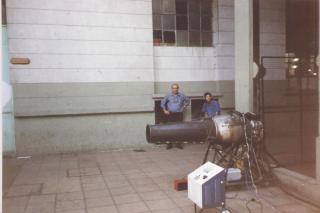
El año que empieza no nos toma desprevenidos y para los muchos detalles que tenemos que pulir contamos con
la promesa de ayuda de más gente que la que ya nos ayudó en el 2000 y a quienes nos sentimos obligados mencionar,
aunque más no sea para que las personas ajenas al proyecto capten algo más de la naturaleza del mismo.
Tenemos varias historias tragicómicas generadas a lo largo del trabajo, pero creemos que el premio se lo lleva
la lata de aceite para turbinas que hizo el viaje Rosario - Buenos Aires, Buenos Aires - Rosario porque las personas que
hicieron la entrega dicen no haber encontrado quién la reciba en la puerta del Colegio....
Y en éste momento sabemos que la lata
está repitiendo el mismo camino. Habrá quién la reciba?. Estará el Krause en la misma dirección o se mudará con destino desconocido?
No se pierda el "Así nos fue en 2001"!...
Nuestro agradecimiento a:
Maestros del taller de Mecánica Ciclo Superior: Sres. A. Seguí, B. González y J. D'Agrosa.
No tenemos tanto espacio para detallar todo lo que les debemos.
Asociación Cooperadora: Fondos para comprar materiales y poder seguir trabajando.
Maestros del taller de Mecánica Ciclo Básico: Sres. J. Kusznieryk, G. Marcone y L. Yance.
Materiales y uso de instalaciones.
Cedit: Sres. E. Soto y L. Córdoba. Uso de instalaciones y colaboración de alumnos de 4to. año en la confección de planos.
Taller de Herrería: A todo su personal; por ayuda, materiales y uso de instalaciones.
Taller de Electricidad: Sres. Dentone y García.
Materiales para el tablero eléctrico y consejos.
Laboratorio de Mediciones eléctricas: Sres Wögerbauer y Álvarez.
Materiales para el tablero eléctrico, instrumentos de medición y consejos.
Taller de Carpintería: Sres Allende y López.
Moldes para tubo de chorro y materiales para el tablero eléctrico.
Taller de Cerámica: Sr. Masi.
Uso del horno para calibrar termocupla.
Taller de Construcciones: Sr. E. Mitkus.
Préstamo de la amoladora de mano para cortar el tubo de chorro y terrajas.
Egresados: Sr. Santiago Rivas. Por estar dos días con nosotros intentando filmar lo que no funcionó.
Sr. Diego Turró. Por el envío de aceite para turbinas desde Rosario. Sres. Néstor Turró y Guillermo Puma. Por fotos del año 1982.
Alumnos: Sres. Joaquín Martínez y Juan Puscama de 4to. año Especialidad Mecánica. Por confección de planos del bastidor
con Autocad.